How does a centrifugal pump work?
Centrifugal pumps are used to pump water, oil and other liquids. How do these pumps work?
Centrifugal pump design
The main elements of a centrifugal pump are the casing and the impeller, which drives the liquid.
The impeller is mounted on a shaft. The shaft can rotate on bearings. The power is transmitted from the motor, most often an eclectic motor, to the shaft.
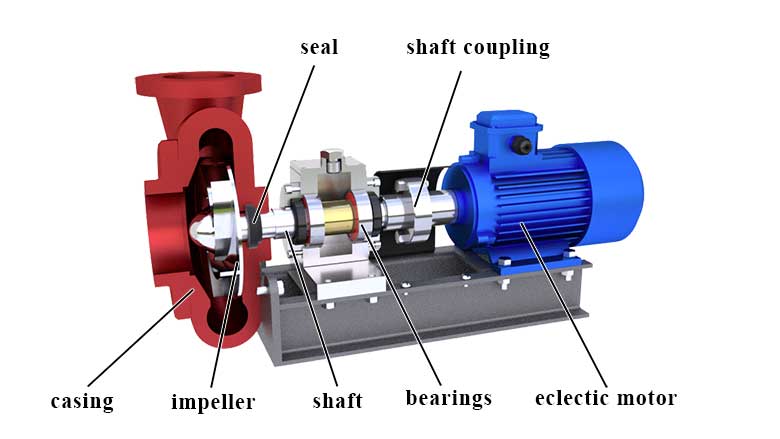
The impeller of the pump rotates, together with the shaft. The vanes in the impeller act on the liquid and make it rotate. The liquid particles are accelerated. As a result of the impact of the vanes, the energy of the liquid flow is increased. The accelerated liquid particles enter the volute, which converts part of the velocity into pressure. The diameter of the passage section of the volute and the discharge nozzle gradually increases. The fluid velocity decreases, and the pressure, according to Bernoulli law, increases.
Impellers design
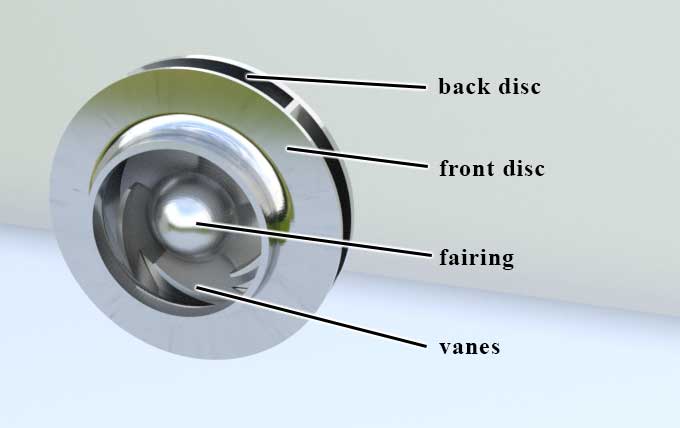
Three main types of impellers are used in centrifugal pumps:
- Closed with back and front discs, vanes and fairings.
- Semi-open with the vanes are free on the front side.
- Open, with the vanes free on both sides.
Double suction centrifugal pump
If bearings support only one side of the shaft, the pump is called a cantilever pump. It is a versatile design that is used in small and medium-sized pumps.
A heavy impeller cannot be cantilevered. In this case, the shaft is mounted on bearings, and the impeller is placed between them.
This construction scheme is well suited for double-suction impellers where the vanes are placed on both sides. A double-suction impeller allows liquid to enter the impeller blades from both sides. Thus, we have two pumping units without significantly increasing the weight and dimensions of the pump. This scheme is relevant for pumps with high capacities because the pumping units are installed parallel.
Multistage centrifugal pumps
By installing pumps in series, the head of the liquid can be increased in the system. Pumps installed in series can be combined by placing several impellers in the same casing. The liquid will go from the first impeller to the second one, from the second impeller to the third one and so on. Using a multistage arrangement can increase the head of the pump many times over, as the impellers are mounted in series, and each of them increases the head.
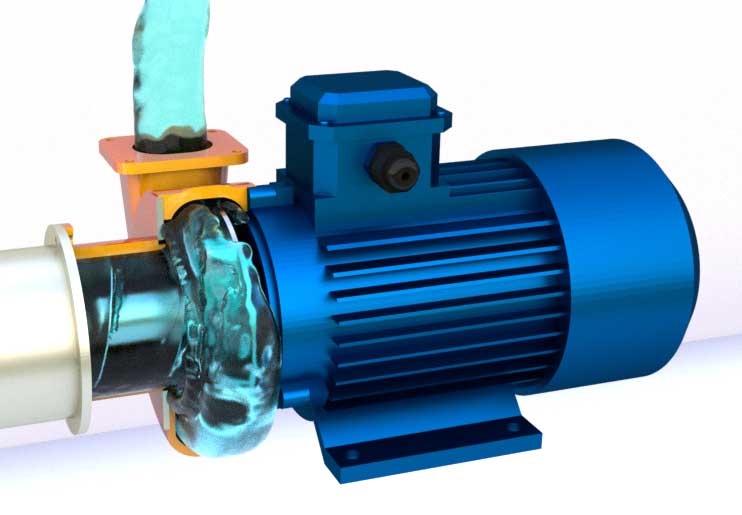
In multistage pumps, different impellers can be used. For example, a screw centrifugal pump has an auger on the first stage and a centrifugal impeller on the second stage.
When the pump is running, the liquid flows continuously into the pump casing through the suction nozzle. But what happens if there is no liquid in the pump? For example, when the pump is first switched on, the pump casing will be empty. For the liquid to fill the pump, the pressure in the pump casing has to be lower than the atmospheric pressure. Then the atmospheric pressure will cause the liquid to fill the casing. To reduce the pressure in the pump, some of the air has to be pumped out of the casing.
Priming
Is an ordinary centrifugal pump able to do this? The answer is no, because the particles move in the pump due to inertia, which depends on mass. The mass of air particles is much lower than that of water particles, so it is impossible to pump air at speeds that a centrifugal pump operates at.
For this reason, centrifugal pumps must be primed before switching on, either through a special channel in the casing or through the discharge nozzle.